2.1 技术难点[3 - 5]
1) 旧复合橡胶沥青路面结合料的低温延度较小, Domix 老化严重, 导致原结合料再生效果不明显, 再生混合料低温弯曲值偏小, 影响混合料的低温抗裂性能。
2) 旧复合橡胶沥青混合料的沥青含量高, 且旧 ARHM 混合料采用粗骨架断级配, 粉料含量多。就地热再生技术添加的新料较少, 对旧有级配的改善空间小; 旧 RAP 较高的粉料含量会导致再生混合料表面油斑较多, 影响沥青混合料的外观和抗滑性能。
3) 各路段沥青含量差异较大, 给混合料目标配合比设计工作带来了较大挑战, 不同路段的再生设计方案需要 “对症下药”, 有针对性地提出新加混合料的类型、 级配要求、 外掺剂比例等。
为解决以上难题, 本研究通过更换外掺剂种类及比例, 改变新添加混合料类型、 比例及级配, 增加或减少沥青用量等, 调整马歇尔试件击实次数等多项方案, 室内成型试件, 对各方案的路用性能进行验证及比选, 最后确定了室内试验实施方案。
2.2 室内试验研究
2.2.1 旧橡胶沥青混合料性能研究
分别在 K55、 K56、 K65、 K66、 K67 进行现场取样, 并对旧橡胶沥青混合料进行相关试验分析。
1) 沥青混合料油石比试验采用离心分离法,橡胶颗粒基本进入集料中, 试验结果如表 1 所示。由表可知, 取样路段旧橡胶沥青混合料的沥青含量差异 性 较 大, 沥 青 含 量 最 小 为 5.1% , 最 大 为5.5% ; 本次就地热再生配合比设计中, 需要针对现场试验路段的沥青含量实际情况, 分段进行设计。
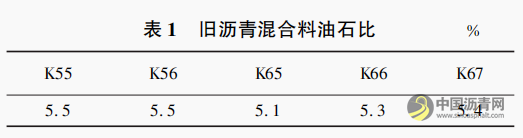
2) 将旧沥青混合料矿料级配分析试验结果绘制试级配曲线, 如图 1 所示。 由图 1 可知, 旧橡胶沥青混合料的矿料级配比较稳定, 各路段变化不大。 本次就地热再生试验研究及现场铺筑试验路段中, 新添加的混合料可以进行统一选择及设计。
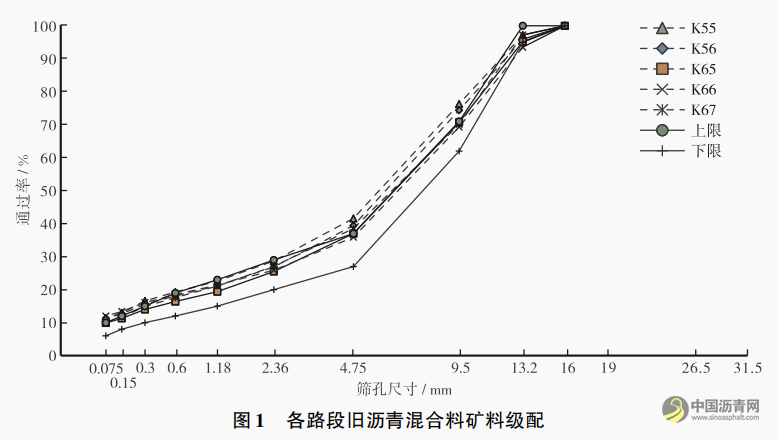
3) 旧沥青的三大指标试验结果见表 2。 由表 2可知, 旧沥青性能老化严重, 针入度及延度远远达不到 《公路沥青路面施工技术规范》 ( JTG F40—2004) 《公路沥青路面再生技术规范》 ( JTG F41—2008) 中的技术要求, 据此应针对性地选择外掺剂以提高旧沥青的性能。
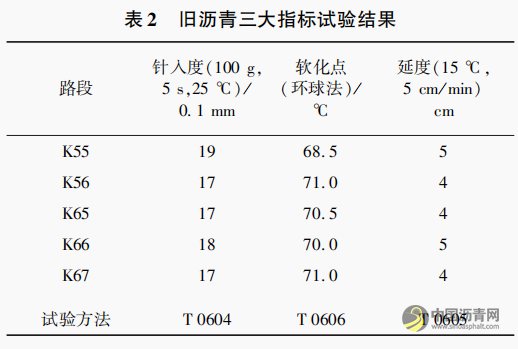
2.2.2 温拌再生剂的选择及添加比例
研究团队选择了目前效果较好的 “ 路路邦BMH 型 (产品 A)”、 “APTL102 型 (产品 B)”、“APT103 型 (产品 C)”、 “ FASIR 温拌剂 (产品D)” 及 “自主研发的温拌再生剂 (产品 E)” 等多种温拌剂或温拌再生剂掺入再生沥青混合料中,进行了一系列混合料路用性能试验。
不同温拌 (或温拌再生剂) 在 7% 掺量下对旧沥青的改善效果试验见表 3, 其高低温性能、 水稳定性性能的试验结果如表 4 所示。
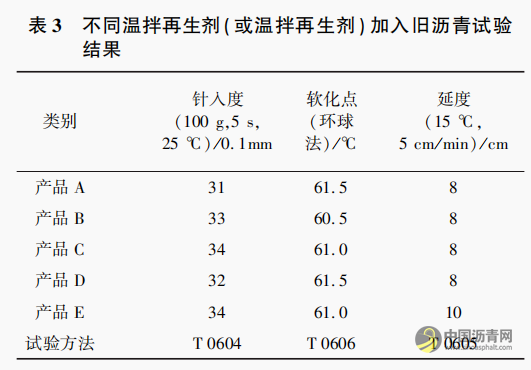
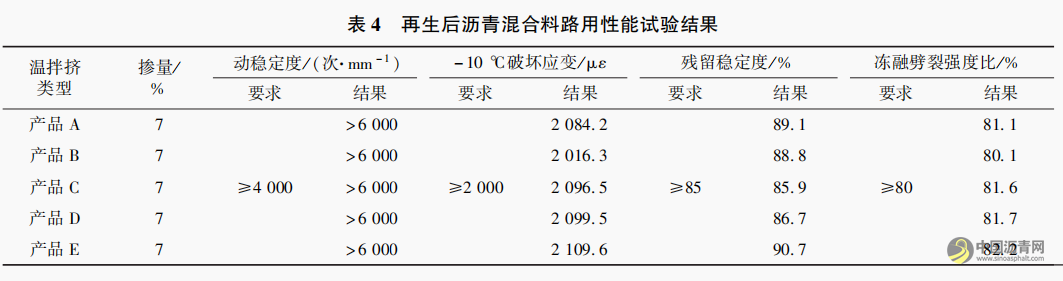
1) 温拌剂的选择。 从试验结果以及车辙试样、混合料拌和效果等因素来分析, 最终选择了和易性较好的产品 E。
2) 试验中存在的问题。 掺加温拌剂或温拌再生剂使旧沥青混合料的和易性、 路用性能出现大幅度提升。 但试验过程中发现车辙试件表面油斑仍较为严重, 并且再生料的和易性差。 温拌剂或温拌再生剂增加了旧沥青混合料的油石比, 同时 “橡胶沥青 + Domix” 双复合改性沥青混合料自身油石比较高、 粉料含量也较高, 导致表面油斑较多[7]。如温拌剂或温拌再生剂掺量少, 则旧沥青混合料的降黏效果差, 施工和易性差, 难以拌匀。
针对上述问题, 本研究根据旧料特点在外掺剂中添加一定量降黏更强的调和油。 该调和油溶解性强, 可对旧料快速降黏, 同时具有易挥发性, 施工过程能快速挥发, 可确保再生料的油石比提高很少,从而避免泛油。 温拌剂和调和油的掺配比例通过旧料拌和后外观、 和易性等确定, 试验结果如表5 所示。

因此选择了温拌剂和调和油的掺配比例为 1 ∶1。 经对掺加 “温拌剂 + 调和油” 的沥青混合料进行大量的试验, 取得了较好的试验效果, 车辙试验试件油斑明显改善。
2.2.3 新添加沥青混合料的选择及试验
由于旧沥青混合料采用双重改性 (橡胶改性 +Domix 改性) , 新料建议采用 SBS 改性沥青。 新沥青混合 料 的 矿 料 级 配 类 型, 选 择 了 新 拌 AC料、 新拌 SMA、 新拌 OGFC、 新拌单粒径改性沥青混合料 几 种 类 型。 鉴 于 沥 青 混 合 料 黏 度 高、粉料含量高 ( 达到 10% 以上) , 通过 10 多种级配及油石 比 的 试 拌、 混 合 料 路 用 性 能 试 验 等,最后确定采用新拌 4 75 ~ 9 5 mm 单粒径改性沥青混合料作为新添加沥青混合料, 解决了混合料易性差、 碾压时容易产生油斑等问题。 合成级配如表 6 所示。

2.2.4 新再生沥青混合料配比研究
为确保施工完后路面标高与原路面标高一致,新混合料用量宜控制在 15% 之内, 以新料级配改善旧混合料中的级配为目标, 确定新旧料掺混比例。 采用 4 75 ~ 9 5 mm 单粒径集料, 油石比 2% ,用沥青胶浆预拌。 新旧混合料中的集料合成级配如表 7 所示。
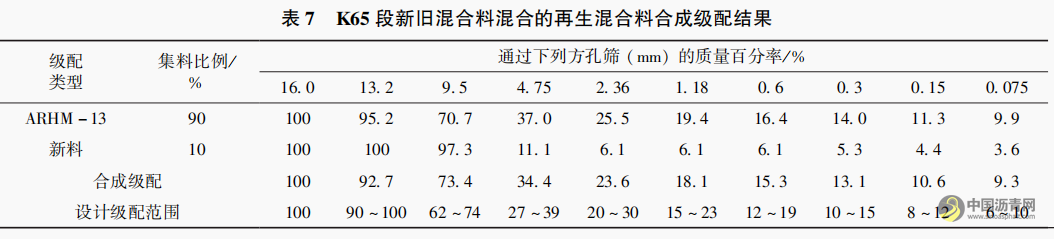
根据上述 K65 段试验结果及相关路用性能验证试验, 确定试验段其他各段新旧料掺混比例。 现场根据压实后路面效果对新加料的比例用量进行及时调整。
2.2.5 再生混合料路用性能验证
首先在试验室 140 ℃温度下成型试件, 发现旧料和外掺剂拌和后流动性变差, 旧料变得黏稠, 再生料变得不容易摊铺。 将温度提高 10 ℃ , 再生料有了较大改善, 通过和施工机组沟通, 3 台加热机组组合可将现场旧料温度加热到 150 ℃ , 因此将室内再生混合料的击实温度选择为 150 ℃ 。 150 ℃ 下的击实试验结果如图 2 所示。
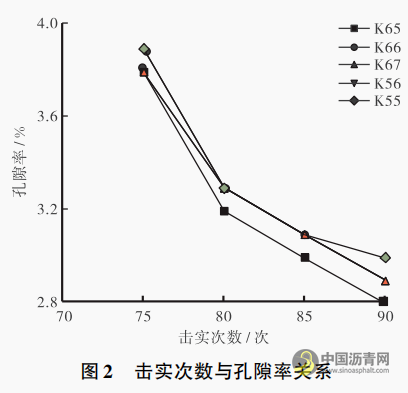
根据图 2 试验结果, 击实次数增加到 80 次及以上, 试件的孔隙率变化趋势减缓。 由此确定用于混合料体积指标设计的试件击实次数为双面击实80 次。 通过此方法确定马歇尔试件密度作为标准密度, 用于评价路面压实度。 并通过此密度成型车辙试件, 对成型后的试件表面进行外观评价及对应的高低温性能评价。
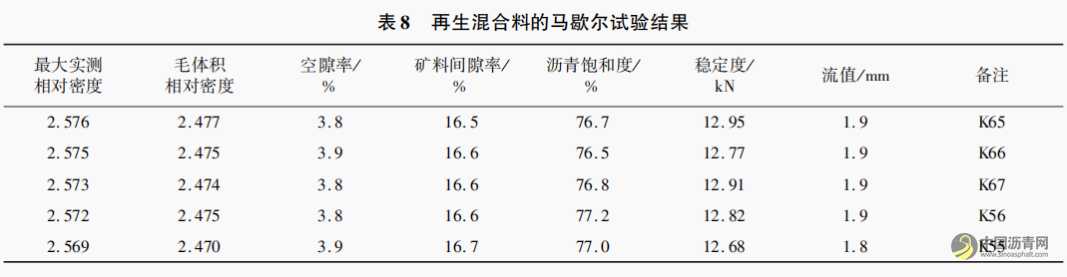
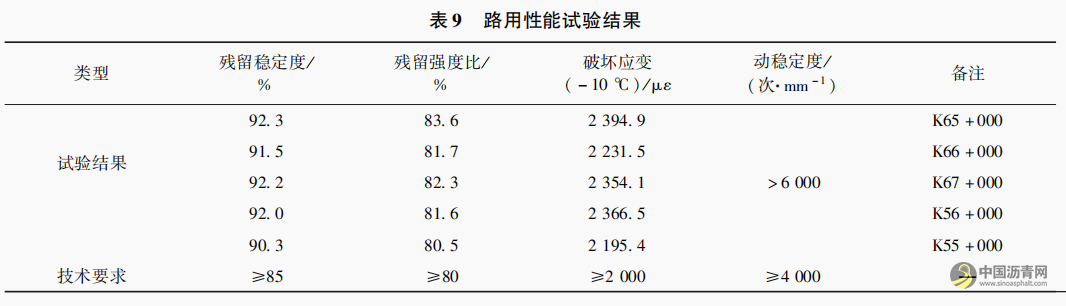
马歇尔试验结果见表 8, 路用性能试验结果见表9。 经过马歇尔试验及相关路用性能试验验证, 再生沥青混合料各项技术指标满足设计规定的技术要求。